界面新闻记者 |
在中信戴卡股份有限公司(下称中信戴卡)长春生产基地的一体化压铸单元内,一台工业机器人正从模具中取出刚完成压铸的铝合金一体化车架,它是汽车底盘的关键组成部分。
经过完整性检查等工序后,这款长宽均在1.4米左右的汽车零部件得以下线。在此之前,它总共经历了13道工序,整个过程不过4分15秒,速度相较传统方式至少提升了30%。
这款一体化压铸的汽车零部件由中信戴卡和中国一汽联合开发,将应用于新款红旗国悦中巴车。中信戴卡为中信集团旗下子公司,是全球最大的铝车轮和铝制底盘零部件供应商。
所谓一体化压铸,是指借助特大吨位压铸机,将近百个分散零部件集成为一个大尺寸零件的制造技术,它采用的是液态铝合金在模具内凝固一体成型的方式,摒弃了汽车行业传统的冲压、焊接工艺。
此前,类似的钢制车架需要98个零部件焊接组装而成。使用一体化压铸技术后,其重量由87公斤减少至58公斤,同时将扭转刚度提升15%。扭转刚度的大小,决定了车身在受到外力时抵抗弹性形变的能力。
厂区内的这套一体化压铸单元去年底投入使用,包括压铸机在内总计有55台套设备,总重量达到550吨,占地1300平方米,相当于五分之一个标准足球场。
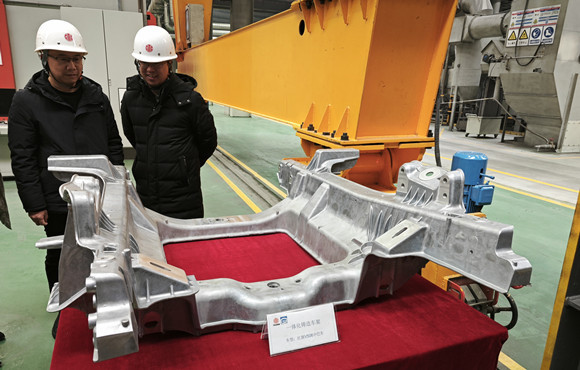
中信集团在2022年立项一体化压铸技术研发,由中信戴卡、中信重工(601608.SH)等旗下公司共同参与,并在今年2月27日正式对外发布技术解决方案,覆盖材料、工艺、模具及装备等多个领域。
中信戴卡技术管理中心材料研究中心主任刘海峰告诉界面新闻记者,面对汽车制造业正在发生的变革,零部件企业必须掌握一体化压铸技术,在这条赛道上占据领先优势。
特斯拉2020年率先使用一体化压铸方式生产了汽车后底板,将70个零部件合而为一,从而实现减轻重量和降低成本。
此后,这项技术逐渐为汽车行业所接受,包括丰田、大众、小鹏在内的汽车厂商均开始类似的尝试。
事实上,一体化压铸并非一项全新的技术,但此前其所能压铸的零部件尺寸相对有限。为了满足特斯拉等汽车公司提出的新需求,压铸机生产商开始生产锁模力更大的压铸机。
锁模力是指压铸机用于锁住模具所输出的力量,这项技术指标将决定它能所能压铸零部件的尺寸。
目前全球知名的压铸机生产商包括中国的力劲科技(00558.HK)、海天国际(01882.HK)和伊之密(300415.SZ),以及瑞士布勒。
在超大型压铸机领域,力劲科技目前的市场份额在九成左右,其已经能够生产锁模力1.6万吨的压铸机,中信戴卡目前的技术覆盖了6000吨-1.5万吨压铸机的需求,已投入使用的压铸机锁模力为7500吨。
全球汽车行业新车型制造周期大幅缩短,是一体化压铸成为新趋势的重要原因。目前,一款新车型从设计到产品量产的周期最快仅为24个月左右,较此前缩短了近一半。
借助一体化压铸,整车和零部件企业可以提高新车型和相应零部件的开发速度。以中信戴卡为一汽集团供应的一体化车架为例,包括模具制作和调试在内,其开发周期在3个月左右,相较传统工艺缩短一半。
不过考虑到一体化压铸产品成本相对偏高,以及汽车行业现有冲压、焊接产线的既有投资等因素,这项技术在汽车制造领域能获得多大程度推广还存在不确定性。
刘海峰透露,中信戴卡后续将推动一体化车架产品在一汽集团新车型的验证和装车,同时也会继续探索一体化压铸后底板、前机舱等其他汽车零部件产品。
除了现有的长春生产基地外,中信戴卡正筹划新建更多一体化铸造工厂,其意向合作客户包括零跑汽车等车企,将根据项目情况适时开展投资建设。
发布评论
评论