亚麻纱线织就的衣物充满自然气息,富有健康色彩,一直以来备受青睐。这种气质独特的植物发源于欧洲,种植历史悠久。欧洲亚麻产业也曾一度辉煌,但从上世纪60年代开始,随着制造用工成本的大幅上升,产业开始逐渐向东方转移。于是在地球的另一面,中国美丽的“江南水乡”浙江、江苏,亚麻纺织业迎来蓬勃发展,为世界亚麻产业历史的延续注入了新的生机。
在这美丽的“鱼米之乡”中诞生的浙江金达集团,起步于丝绸,转型于亚麻,现今作为亚麻纺织领域的领军者,在发展过程中,同样也遭遇了制造成本增加、产量很难提升的瓶颈。
金达集团的执行董事兼总经理沈跃明表示:“在纺织领域,亚麻产业小,用工多,设备陈旧。要想继续生存,就必须在现有基础上提高自动化和数字化水平,减少用工、降低成本、提升效率!于是,我们决定和西门子合作。”

制造成本和产量瓶颈只是外压,更重要的内因则是金达觉得自己有责任改变行业现状,让亚麻纺织摆脱低端的烙印,提升至自动化、数字化、信息化的新水平。所以它才迫切的需要寻找途径,把亚麻纺织产业从古典的“江南婉约女子”改造成时尚的“现代摩登女郎”,而西门子无疑是这条改造之路上的最大助力。
把脉工厂,抽丝剥茧
其实早在几年前,金达就已经开始从能源管理项目着手,对工厂改造进行了初步尝试,最初选择西门子作为合作伙伴,是看中了其品牌知名度和良好口碑。而后在锅炉控制系统的实际改造中,节煤率15%,节电率26%的突出成效,更让金达充分感受到西门子过硬的专业能力和负责的做事态度。
所以这次产业升级、构建数字化工厂的重任,金达同样希望和西门子共同来完成。2013年初,西门子团队入驻金达亚麻工厂,开始了抽丝剥茧的咨询规划,经过一番梳理,发现了两大问题。
首先,工厂中的产线处于“黑箱”状态。表面上,生产在有条不紊的进行,可是若想知道生产计划的具体信息,比如原材料用了多少?生产进行到了什么程度?有多少销售订单?根本没法立刻给出答案。
在这种“黑箱”状态下,一旦生产设备出现故障,机器重修、多修、不及时修的情况就会拖慢运转效率,严重时甚至会影响正常生产。更重要的是,若想对物料、质量、销售进行追溯,则是完全不可能的。
其次,管理模式相对粗放。一些重要的生产数据,比如质量数据被随意写在纸条上,短期之内还能看到,长期而言查找非常不便。同样,人事部门在月底核算绩效和奖金时,也只能看书面记录或是听员工口头描述,这给薪资的发放造成了极大的不便,还容易产生纠纷。
把脉出这两个痛点后,西门子深知要对症下药—既要解决产线自动化,又要实现管理透明化。经过精心设计,专家们决定从位于浙江省嘉兴市横港镇的金达老厂开始,逐步构建制造执行系统(MES)。
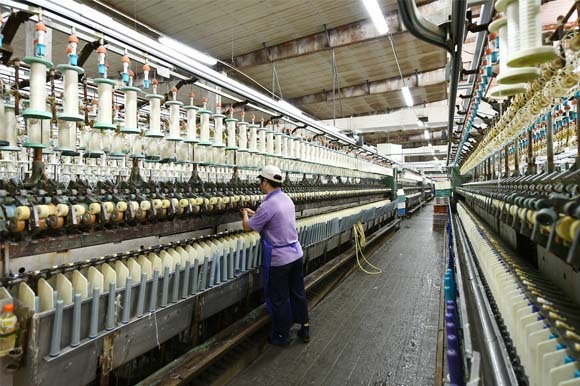
软件为基,管理为核
MES是面向制造企业车间执行层的生产信息化管理系统。它能够加强生产物料需求计划的执行功能,把物料需求计划通过执行系统同车间作业现场控制系统联系起来,实现这一点的关键就在于MES可以提供各部分的管理模块。所以,西门子专家到达老厂的第一要务,就是对亚麻纱线的整个生产周期进行梳理。
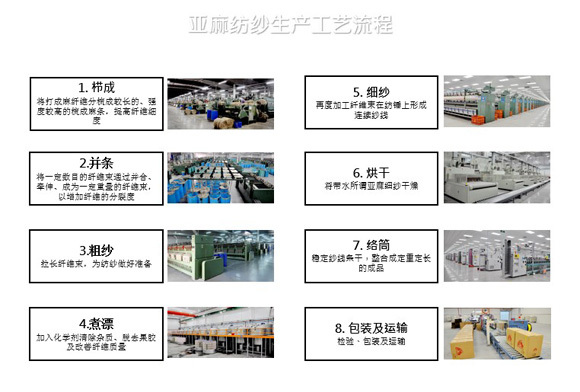
但是这第一步就遇上了极大的挑战—亚麻纺织生产工艺包含栉成、并条、粗纱、漂煮、细纱、烘干、络筒、包装及运输这八道工序,每一道流程都应该参照规范有序进行,但现状却是经验在主导生产。比如亚麻纱线的生产配比。亚麻原材料来自比利时、法国以及中国新疆等地的农田,每一批次的性质都有一定差异。那么生产特定规格的产品时各种亚麻的用量究竟需要多少?以前的金达只能靠人来解决—配比员依据自身的经验观察原料的色泽、质地,以此决定原料配比。这就造成系统的随机性太大,无标准和规范可言,MES将变成空中楼阁。
“要是源头上都混乱了,那之后追溯的意义也就不大。”金达集团质保安全部主管,同时也是数字化工厂项目总协调的沈益飞对这个问题有十分深刻的认识。在西门子的建议下,金达购置了专业的检测设备,能够对原料的物理特性进行精准的检测。在系统运行一段时间后,配比员发现所有的原料大概可以分为六个档次,不同档次的原料又可以组合成三套以上的标准配方。检测结果将直接提供给MES系统,让采购部能对原材料进行清晰的划分,之后的生产计划才能井然有序地进行。
于是,让整个纺织业都头疼的原料配比难题就这么迎刃而解。经过一年多的努力,西门子帮助金达梳理出了包括计划管理、质量管理、设备管理、物料管理和作业管理在内的五大主要管理模块和50多个业务流程,相对应的关键功能点足有56个。
这些管理模块正是生产标准化和构建MES的核心,西门子MES系统完全符合ISA-95标准,能够降低与ERP集成的成本,还能与产品生命周期管理软件协同工作,提供生产能力和状态,提高了生产制造的灵活性。
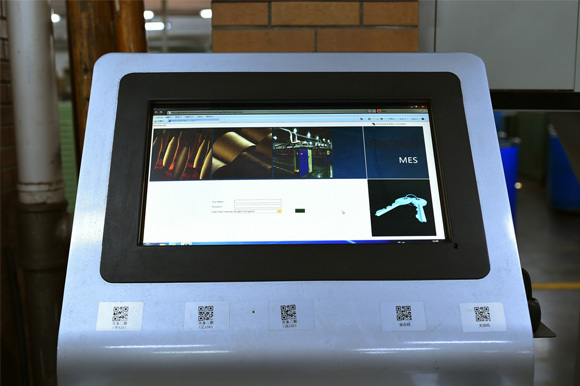
生产透明,管控精细
构建数字化工厂的路途才刚刚开始,更多的问题接踵而至。
首先,金达老厂设备落后,很多老旧的设备根本没有数字采集系统。数据都采集不了的话,又谈何数字化?谈何生产透明化?
为此,西门子对老厂的部分设备进行了升级改造,借助传感器和工业通信网络,填补了老旧设备的数字采集能力。把底层设备数据连入MES,自下而上打通工厂内部的信息流。
其次,在MES的推行过程中,由于一线操作人员多是老员工,要他们直接操作现代化设备困难很大,这相当于要改变他们20、30年以来的工作习惯,很多人都感觉手足无措。
对此,西门子的专家为一线员工进行了大量的精益生产培训,对于操作要求比较高的岗位进行分流,那些不愿意改变的人就被分流到其他岗位上去。除此之外,工程师还在系统的界面和操作方式上下了功夫,大部分的输入操作都被改成了扫描二维码,简单高效。
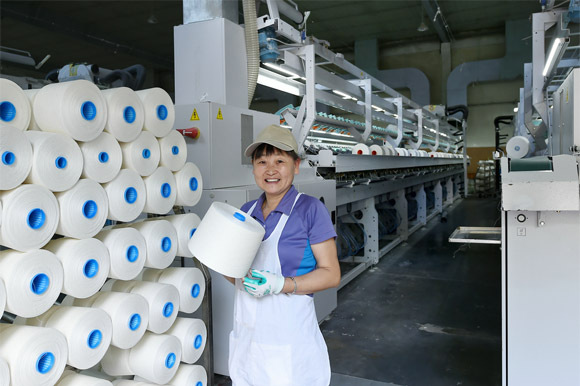
兵来将挡,水来土掩,一个又一个的难题被攻克下来。在MES系统试运行阶段,工厂的生产效率和管理水平都有了明显的提升。
首先是物料管理,哪些原材料需要采购,哪些还没有用完,现在都能随时获悉,这提高了亚麻的资源利用率,加快了在制品流转。
在生产计划方面,所有的生产数据都被有序的储存在MES系统中,打开系统界面,就能清楚地看到生产进行到了什么程度?销售订单有多少,还有多少没有完成?管理层想要数据,点击手机APP即可获悉。数据不但使得各生产环节透明化,还能帮助管理层更加科学地做出决策。
在作业管理方面,标准化业务流程使作业管理更加精细。不像以往把作业现场的检查结果写在纸上,工厂的管理人员开始使用iPad记录数据,检查完后打印整改清单,使得整改更有成效。
在质量管理方面,每一批次每种规格的产品质量都要接受检验,都要有数据,通过对生产过程中的关键环节进行严格质量监控,从而提高产品质量。当出现客户投诉的情况,管理层就可以随时追溯全年每一次的生产批次,以及当时生产的质量情况。这在追溯方面是质的飞跃!
还有重要的设备管理,有了设备管理模块后,系统按照设备周期、设备运行情况进行任务排程和设备维修保养排程。在设备上找到一些冗余环节,以提高设备利用率,减少故障,保证生产。
自此,生产各个环节变得透明;管理变得精细化、标准化,一切都有章可循。
数字工厂,精益践行
除了横港老厂的改造升级,在几十公里以外的海盐,金达全新的数字化工厂也在同期建设之中。这背后,自然少不了西门子中国研究院顶级顾问们的通力支持。在他们眼里,构建数字化工厂不只是软硬件技术升级,更是生产信息系统与自动化体系的完美集成,建立企业运作流程体系才是数字化转型的核心关键。
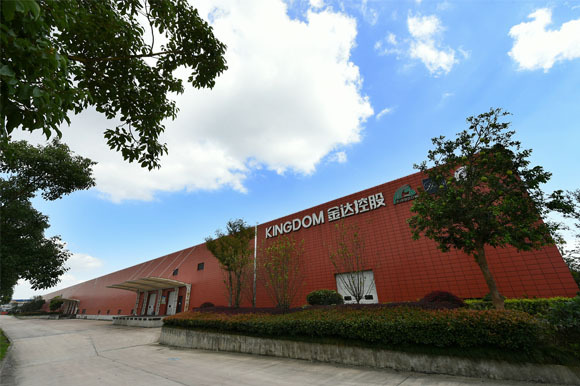
利用可以简化并加速实施过程、提高生产力、加强协同的Teamcenter软件,西门子专家们构建了虚拟仿真工厂,参与了海盐新厂的全部规划建设—既包括网络架构、现场通讯、接口、设备信息化定义在内的信息化布局,又包括EPC、工艺、物流在内的机械布局。
在具体建设中,新厂里所有的变频器都使用了Sinamics S120,这是西门子推出的全新的集V/F控制、矢量控制及伺服控制于一体的驱动控制系统。该系统不但具有高度灵活的模块化设计,即允许不同功率等级与控制性能的单元自由组合;还支持“一网到底”的通讯技术,上位通讯支持标准的PROFIBUS DP现场总线或工业以太网PROFINET;“一心多用”的多机控制技术让一个控制单元就可同时控制多达多台逆变和一台整流,所需数据都保存在控制单元中,保证系统高效可靠运行。除此之外,新厂使用的所有电机都是高效节能电机,漂煮工序中的锅炉也按照老厂进行了改造,每年节省成本300-500万元。这一系列的建设再结合利用B.Data软件构建的能源管理监控系统,使得新厂整体的用水量下降了20%,用电节约了10%。
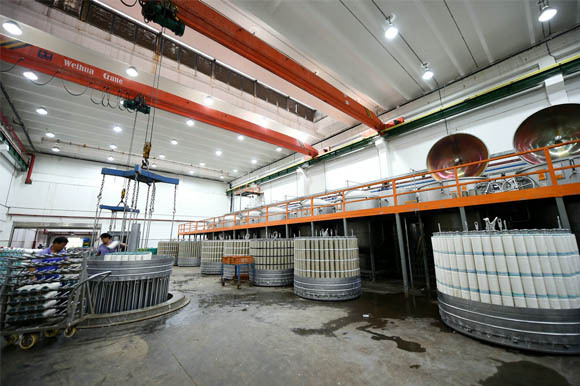
沈跃明对此给予了高度评价:“从新工厂的规划上来看,无论是布局、安全性还是节能,都达到了我们的预期,尤其是节能,令人惊喜。”
新厂目前的员工人数只有老厂的1/3,自动化程度非常高,可以说是成为了面向“工业4.0”的数字化工厂。无论是老厂的改造还是新厂的建设,西门子希望通过数字化技术,把精益管理的理念像种子一样播撒到亚麻产业的土壤中去。
从浙江到江苏,从新疆到黑龙江,从埃塞俄比亚到欧洲,金达前进的脚步从未停止。而西门子,作为金达在全球扩张之路上的合作伙伴,将用信息化和数字化做武器,带领金达始终走在行业前列,迎接新一轮工业浪潮。
评论